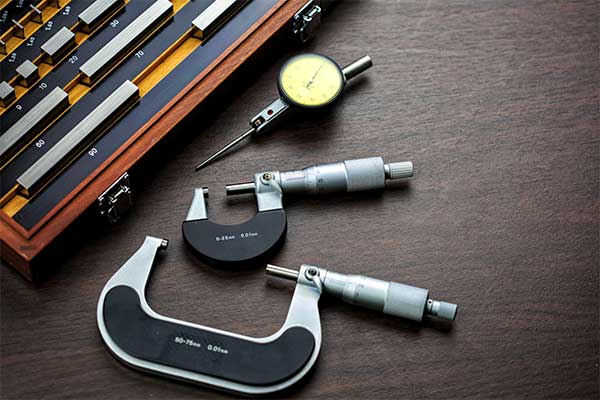
Calibration
In measurement technology calibration is the comparison of measurement values delivered by a device under test with those of a calibration standard of known accuracy.
Such a standard could be another measurement device of known accuracy, a device generating the quantity to be measured such as torque, pressure, voltage, sound or a physical item, such as a metre ruler.
Outcome of the comparison can result in one of the following:
- No significant error being noted on the device under test
- A significant error being noted but no adjustment made
- An adjustment made to correct the error to an acceptable level
- Failure to comply. This outcome is due to being out of tolerance. This will result in the item being isolated and withdrawn from service
The calibration standard is normally traceable to a national standard held by a national body.
Basic calibration process
The calibration process begins with the design of the measuring instrument that needs to be calibrated. The design has to be able to "hold a calibration" through its calibration interval. In other words, the design has to be capable of measurements that are "within engineering tolerance" when used within the stated environmental conditions over some reasonable period of time. Having a design with these characteristics increases the likelihood of the actual measuring instruments performing as expected
The purpose of calibration is for maintaining the quality of measurement as well as to ensure the proper working of particular instrument.
Full certification is produced including certificates and registers for the equipment which has been tested.